When selecting a metal roofing product, there is an expectation that it will perform as intended over the life of the building. But what assures building owners, code officials, or design professionals that a product will in fact perform as promised? This question often comes up in building product discussions and the accepted way to answer it is to subject the products to physical testing. The type of testing is usually very specific to the product based on protocols and procedures developed by independent agencies such as Underwriters Laboratories (UL), ASTM International, or others. Manufacturers typically submit their products to independent testing labs who follow these standard test procedures. Once testing has concluded, they report the results back to the manufacturer. These results then show whether the product meets stated performance criteria or not. If not, the manufacturer can re-design and re-test until it does and then make the final results available to the public.
For metal roofing, a series of relevant and important tests are typically performed. In this blog, we will look at two of them related to structural performance and wind uplift.
ASTM E1592
The structural integrity of metal roofing is crucial given the various natural forces that can be imposed on the materials. Effects from wind, snow, or other conditions can compromise its integrity. Accordingly, the ASTM Committee E06 on Performance of Buildings (including sub-committee E06.57 on Performance of Metal Roof Systems) has developed ASTM E1592 “Standard Test Method for Structural Performance of Sheet Metal Roof and Siding Systems by Uniform Static Air Pressure Difference”. While the standard acknowledges the use of computation (i.e. calculations) to determine the basic structural capacity of most metal products, it also points out that some conditions are outside of the scope of computational analysis and hence need to be tested.
The standard describes a test method with “optional apparatus and procedures for use in evaluating the structural performance of a given (metal) system for a range of support spacings or for confirming the structural performance of a specific installation”. As such, it is very specific both to metal roofing and its installation. This test method uses imposed air pressure not to look at air leakage but simply to determine structural reactions. It consists of three steps:
1. Sealing the test specimen into or against one face of a test chamber
2. Supplying air to, or exhausting air from, the chamber at the rate required to maintain the test pressure difference across the specimen
3. Observing, measuring, and recording the deflection, deformations, and nature of any failures of principal or critical elements of the panel profile or members of the anchor system
The test needs to be performed with enough variation to produce a load deformation curve of the metal and account for typical edge restraint (fastening) representative of field conditions.
Manufacturers need to submit different products that are tested at least once at two different span lengths between supports. Standing seam roof panels are typically tested at a 5’-0” and 1’-0” span. Spans between the two tested spans can be interpolated. The result is a table of tested loading results that can be compared to code required or engineered design loading to then determine if the selected material and spacing are adequate for the project needs or if another product or spacing is needed.
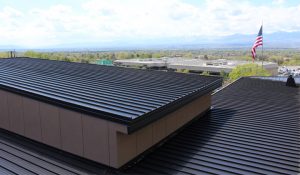
UL 580
The ASTM E1592 test is focused on the structural integrity of metal panels. It also uses positive and negative air pressure in a static (i.e. non-moving) condition to determine performance. There is also a separate concern about how metal roofing will perform in a dynamic condition as would be expected in a windy condition where wind gusts can ebb and flow erratically. In that regard, a separate test developed jointly between Underwriters Laboratories (UL) and the American National Standards Institute (ANSI) looks at the ability of roofing to resist being blown off a building due to wind. Known as ANSI/UL 580 “Standard for Tests for Uplift Resistance of Roof Assemblies”, it has become the recognized means to identify and classify the suitability of roofing for different wind conditions – low to high.
This test is also specific in its scope and intent stating that it “evaluates the roof deck, its attachment to supports, and roof covering materials”. It also points out that it is not intended to test special roof conditions, main or secondary structural supports, or deterioration of roofing. The standard prescribes in considerable detail the type of test chamber that needs to be constructed and used for the testing which includes three sections: “a top section to create a uniform vacuum, a center section in which the roof assembly (i.e. deck, attachment, and roofing) is constructed, and a bottom section to create uniform positive pressure”. The test procedure is then based on placing the roof assembly into the test chamber and subjecting it to a prescribed sequence of 5 phases of oscillating positive and negative pressure cycles (simulating dynamic wind conditions) over 80 minutes of total testing.
There are four wind uplift classifications obtainable for a tested assembly based on the test assembly retaining its attachment, integrity and without any permanent damage. These include Class 15, Class 30, Class 60, and Class 90. Each class has its own requirements for test pressures with increasing pressure as the class number increases. Higher class numbers indicate increasing levels of wind uplift resistance. Note, that to obtain a Class 60 rating, the tested assembly must pass the Class 30 test then be immediately subjected to the Class 60 test sequence. Similarly, to obtain a Class 90 rating, the tested assembly must first pass both the Class 30 and 60 tests. Metal roofing manufacturers who want their roofing products tested and classified under UL 580 must pair them with standard roof deck and fastening materials. Hence most have many different tests performed and results reported accordingly.
When reviewing metal roofing options, it is comforting to know that most manufacturers have tested their products and designed them to meet or exceed minimum requirements. To find out more about tested results of products you may be considering, contact your local MBCI representative or see the MBCI website and select the “testing” tab under a selected product.