Tag: energy efficiency
Metal Roof System Retrofit Benefits
Looking Ahead: 2022 Trends at a Glance
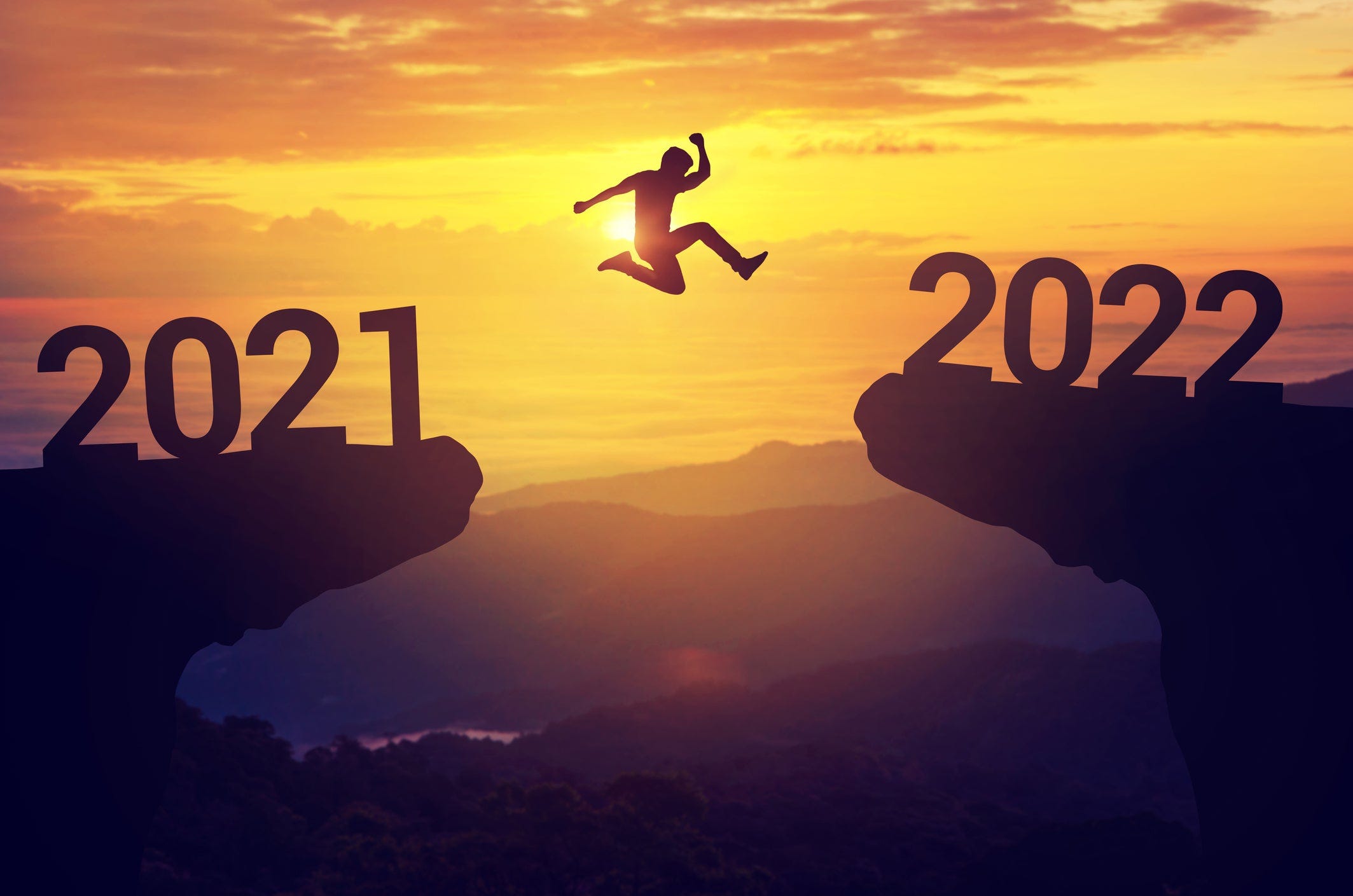
Why Upgrade a Roof to Metal Panels?
Metal Panel Roof Restoration & Installation
Are Metal Panels An Ideal Low-Slope Roofing Material?
Many large, commercial, low-rise buildings often don’t benefit from steeply-sloped roofs the way residences and small commercial buildings might. This is because a steep roof slope would add unwanted height and unnecessary construction cost. Buildings like warehouses, retail stores, etc. are more appropriately built with low-slope roofing, commonly known as “flat roofs”. The National Roofing Contractors Association (NRCA) defines low-slope roofs as those with “a slope at or less than 3:12″. Anything steeper qualifies as a “high-slope roof”. With this in mind, let’s look at some key points to consider when designing and constructing a low-slope roof.
Low-Slope Roofing Materials
When it comes to selecting low-slope roofing products, there are generally three fundamental choices:
- Asphalt/ Bituminuous Products: The traditional commercial roofing norm for many years, the use of asphalt/bituminous products has dwindled as newer, more appealing options have emerged.
- Flexible Membrane Roofing: This roofing material can be made from a variety of types of plastic/polymer-based materials (commonly known as EPDM, TPO, PVC, etc.). Rolls of the chosen membrane are laid out on the roof structure and secured in place either with mechanical fasteners (screws with large washers) or with a continuous layer of adhesive.
- Metal Roofing: Sometimes overlooked, metal roofing is suitable for different roof slopes. Many metal roofs that use standing-seam systems are rated for use with a pitch as low as ½:12.
When considering which type of roofing material to use for a building project, there are a number of significant differences that illustrate why metal roofing is often the ideal choice.
Engineered For Superior Performance
Standing-seam metal roofing is made specifically for use on low-slope roofs as it meets a number of performance requirements:
- Water resistance: Precipitation doesn’t penetrate through metal or through the standing seams where the metal panels join together. This is why they can tolerate such low slopes, allowing the water to drain away slowly and predictably without leakage.
- Rigidity: The rigid nature of metal means that there is less opportunity for ponding (standing water). This is not always the case with asphalt/bituminous or membrane roofing systems.
- Drainage: Metal roofs carry water to the building’s edge toward gutters and downspouts that carry it away from the building. Other roofing systems rely on drainage piped inside the building. This takes up space and has the potential to leak water inside the building and cause damage.
- Wind Resistance: Standardized uplift testing shows that metal roofing performs as well or better in extreme weather than mechanically-fastened or fully-adhered membrane systems.
- Durability: The most cited advantage of metal roofing is its long-term strength and durability. Engineered design and use of high-quality coatings ensures a longer lifespan—50 years or more. In contrast, other roofing types typically feature lifespan ratings of 20 or 30 years.
- Puncture Resistance: Low-slope metal roofing is more puncture-resistant than asphalt/bituminous or membrane roofing. This makes it better able to tolerate foot traffic, hail and other puncture-inducing hazards.
- Construction/ Installation Ease: Metal roofing panels are custom-made to suit specific building sizes and end uses. This customization typically means it takes less time to place and install metal roofing in the field. Further, metal panels can tolerate a wide range of temperatures and weather conditions and still install and perform as intended. Low-slope roofs are also safer to walk on with less risk of slips, falls and other hazards.
Cost-Effectiveness
Using metal roofing on low-slope roofing systems can be cost effective in a number of ways:
- Fewer labor hours as a result of the ease of installation saves money during construction.
- Competitive material costs, particularly if the metal roofing is part of a total metal building package from a single manufacturer.
- Minimal maintenance requirements and aversion to rusting, mold growth and decay that save the building owner money over time.
This all adds up to a very favorable life-cycle cost.
The performance, cost-effectiveness and life-cycle benefits of metal roofing panels make them a viable option for low-slope roofing systems. Manufacturers like MBCI can help you select the right metal roofing products and provide information and resources to help ensure proper installation.
View examples of low-slope metal roofing projects and contact your local MBCI representative to start your project today.
Understanding LEED for Green Metal Buildings
Designing and constructing sustainable buildings has become a mainstream expectation of most building owners. Whether for reduced energy costs, higher returns on investment, or as an organizational philosophy, “green” building solutions are in demand. Perhaps the best known and most often cited program to achieve these goals is the US Green Building Council’s (USGBC’s) LEED® rating system. While some may think that green buildings are more complicated and costly to build, that is not actually the case. This is especially true when metal building materials are used. In fact, metal buildings are an ideal and economical way to pursue sustainability goals and LEED certification. How? We break it down as follows:
The LEED® Program
The LEED program has been in use since 1998 and is now used worldwide. It is a voluntary, point-based rating system that allows for independent review and certification at different levels. These levels include Certified (40-49 points), Silver (50-59 points), Gold (60-79 points), or Platinum (80 or more points). Since it allows for choices in which points are pursued, innovation and flexibility are entirely possible as long as specific performance criteria are met. It also encourages collaborative and integrative design, construction and operation of the building.
Points are organized into six basic categories, many of which can be addressed through metal building design and construction, as summarized below.
- Location and Transportation: Metal buildings can be manufactured and delivered to virtually any location. That means they can support LEED criteria for being located near neighborhoods with diverse uses, available mass transit, bicycle trails, or other sustainable amenities. Metal building parking areas can also be designed to promote sustainable practices for green vehicles and reduced pavement. This all contributes toward obtaining LEED eligibility.
- Sustainable Sites: Adding a building to any site will certainly impact the natural environment already there. Delivering portions of a pre-engineered metal building package in a sequence to arrive as needed means that the staging area on-site can be minimized—reducing site impacts. Additionally, using a “cool metal roof” has been shown to reduce “heat island” effects on the surrounding site and also qualify for LEED.
- Water Efficiency: Any design that reduces or eliminates the need for irrigation of plantings and other outdoor water uses is preferred. Incorporating metal roofing with gutters and downspouts, as is commonly done on metal buildings, allows opportunities to capture rainwater for irrigation or other uses. It also helps control water run-off from the roof and assists with good storm water control.
- Energy and Atmosphere: Metal buildings can truly shine in this category. Creating a well-insulated and air-sealed building enclosure is the most important and cost-effective step in creating an energy conserving building. A variety of insulation methods for metal building roof and wall systems are used to achieve this. Typically, metal building construction uses one or more layers of fiberglass insulation and liners combined with sealant and air barriers. Alternatively, insulated metal panels (IMPs) provide all of these layers in a single manufactured sandwich panel with impressive performance. Windows, skylights and translucent roof panels can provide natural daylight, allowing electric lighting to be dimmed or turned off. For buildings seeking to generate their own electricity, standing-seam metal roofing provides an ideal opportunity for the simplified installation of solar photovoltaic (PV) systems. Metal roofs generally provide a sustainable service life in excess of 40 years. This means they can outlast the PV array, thus avoiding costly roof replacements during most PV array lifespans.
- Materials and Resources: Life Cycle Assessments (LCAs) are recognized by LEED as the most effective means to holistically assess the impacts that materials and processes have on the environment and on people. Fortunately, the Metal Building Manufacturer’s Association (MBMA) has collaborated with the Athena Sustainable Materials Institute and UL Environment to develop an industry-wide life cycle assessment report. There is also an Athena Impact Estimator that can help with providing LEED documentation. Metal buildings support exceptional environmental performance through the significant use of recycled steel and the reduced need for energy intensive concrete due to lighter weight buildings.
- Indoor Environmental Quality: Most people spend much more time indoors than outside, which impacts human health. Therefore, LEED promotes or requires using materials that don’t contain or emit harmful substances. It also promotes design options for natural daylight, exterior views and acoustical control to promote psychological and emotional well-being. Metal buildings are routinely designed to readily incorporate components that help achieve these indoor qualities.
In addition, some LEED points are available for demonstrating innovation and addressing priorities within a geographic region.
Considering the qualities listed above, metal buildings clearly provide a prime opportunity to pursue LEED certification at any level. To find out more about the LEED rating system, visit https://new.usgbc.org/leed. To find out more about successfully designing and constructing metal buildings pursuing LEED certification, contact your local MBCI representative.
Design and Performance Benefits of Insulated Metal Panels
In a prior post on insulated metal panels (IMPs) we reviewed some of the basic things everyone should know about this versatile and lightweight metal building component. In this posting, we will drill down a bit more on the benefits of incorporating IMPs into a new or retrofit construction project. Here are some of the top reasons they are so popularly used in both walls and roofs:
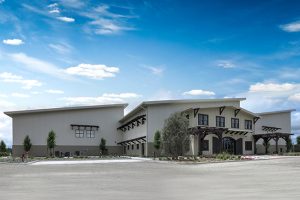
Energy Conserving, Space Saving Insulation
Foam plastic insulation is used between the metal skins of IMPs. Such insulation has been accepted for use by building codes for quite awhile provided it meets certain conditions. IMPs have been tested and shown to meet or exceed all code requirements for construction and for energy conservation too. Part of their appeal over other ways to insulate is that they can achieve high performance in a thinner wall or roof assembly than would be required with other types of insulation, such as fiberglass. IMPs are available in thicknesses that range from 2 to 6 inches and have corresponding R-values from R-14 to R-46 allowing design professionals to select the thickness that matches the energy performance level sought in a particular building. Other insulation types would require thicknesses of at least twice as much to approach the same R-values as IMPs. Further, the metal interior and exterior skins are the only finish material needed so the total panel thickness is very space efficient. Thinner IMPs in the walls and roofs can save space in the building or on the site all while achieving high energy performance.
Durability, Longevity, and Low Maintenance
The manufactured panels are rigid and quite strong. They have been tested for compression, tensile, and shear strength with impressive numbers that come about because of the combination of the rigid foam and steel properties. The surfaces are made from the same long-lasting galvanized and factory finished steel used in other metal wall and roof panels so their resistance to weather, abuse, and even harsh conditions has been proven, making them very easy to maintain. In locations where severe weather and storms are a concern, they can also be specified to meet requirements for heavy winds, hail, and similar concerns. Plus, since the skins of the IMPs are made of noncombustible steel, they provide an ignition barrier as part of an overall fire protection scheme for the building.
Cost Saving Construction
IMPs are an “all-in-one” product that takes the place of many other products and components used in traditional construction. Instead of requiring multiple trades and materials to be installed individually over some number of weeks, IMPs are installed by a metal building contractor and allow the walls and roof to be completely closed in with a single trade. The use of concealed fasteners in the side joint of the panels makes installation quick and easy. Unlike other construction systems, the inherent strength and resiliency of IMPs means that work doesn’t need to stop over weather concerns. All of this saves a considerable amount of labor costs and can also save a lot of time meaning buildings can be completed quicker and more economically. It could also mean that an owner is able to occupy and use the building sooner, thus reducing construction financing costs and allowing operations to begin more quickly.
Versatility for Use in Many Building Types
IMPs can be used in virtually any type of new construction and for many retrofit applications too. There is a range of modular panel sizes that can work successfully with different structural elements of the rest of the building. The finished profiles and colors can all be selected to match the design needs of the building with edges, corners, and trim details all based on simple, appealing aesthetics. There are even IMPs specially designed for cold storage or refrigerated space applications. These panels may be part of the building exterior or create an isolated space within a larger building. Either way, they are designed for the rigors of a high use installation.
With such a broad range of benefits and capabilities, you owe it to yourself to check them out for a building project that you may be involved in. The best place to start is by contacting your local MBCI representative, and by signing up for our newsletter to subscribe to our blog.
What You Need to Know About Insulated Metal Panels
Insulated metal panels (IMPs) are “lightweight, composite exterior wall and roof panels with metal skins and an insulating foam core” as defined by the Metal Construction Association (MCA). The outer skin serves as either metal wall siding or metal roofing using standard profiles, while the inner face serves as a metal interior finish or liner. The rigid insulation between the metal skins gives the panels their superior energy conservation properties and also provides a rigid core for extensive spanning capabilities across structural members.
With this basic make-up in mind, here are a few things you should know about using IMPs in a metal building project:
Building Types
Virtually any building being designed as a metal building should consider the use of IMPs. This includes all types of commercial, industrial, institutional, recreational and government buildings. More specifically, IMPs have been used very successfully on manufacturing facilities, schools, retail centers, offices, warehouses, power plants and many other building types.
Insulated Roofing and Walls Assemblies
IMPs serve as a complete wall or roof assembly. That means they can provide cladding, insulation, a water-resistant barrier, an air barrier, and finished surfaces all in one panelized product – essentially everything but the building structure upon which they are installed. These characteristics are true for conventional buildings as well as for specialty construction types such as the climate controlled processing, storage, or distribution of perishable food or other items. With panel thicknesses commonly available from 3 inches to 6 inches, walls and roofs can be designed to meet the specific thermal performance requirements of virtually any building need.
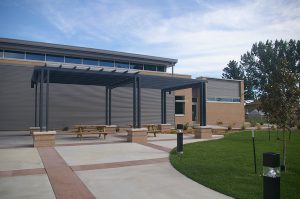
Architectural Design
IMPs are available in a wide variety of colors, widths, profiles and finishes, enabling virtually any aesthetic desired for walls and roofs. Further, architectural IMPs provide the freedom to address building-specific or unique circumstances with options such as custom shapes and widths, special custom colors and finishes, custom fabrication including, but not limited to bent corners, curved panels, and trimless ends. Architectural IMPs also offer options to integrate with windows, louvers, sunshades or other similar products to offer total building envelope solutions.
Panel Joints
Most IMPs are fabricated with the intention of working together as a complete system. That means attention has been paid to the design of the edges so the panels can interlock and be sealed to form a continuous joint that is water tight and air tight. In some cases panels may need to overlap, such as on long roof runs over 50 feet, but manufacturers have worked out those details to help assure the roof or wall performs as intended. Based on this, properly-installed IMP systems generally come with a very long warranty period.
Ease of Installation
The fact that IMPs are a single, finished, rigid panel, makes them quicker to install than other multi-product and multi-step assemblies. This translates to obvious labor savings and some material cost savings compared to other systems. Further, the simplified installation process has been shown to limit exposure to accidents, helping create a safer, more efficient work flow. It can also mean that construction time schedules are easier to meet or even beat.
To find out more about IMPs and ways to use their full characteristics and capabilities on a building you are working on, contact your local MBCI representative.
Reducing Peak Demand Costs with Cool Metal Roofs
Among the many benefits offered by cool roofs—including a decrease in urban heat island effect or increased roof system longevity—perhaps the most significant is a reduction in peak demand energy usage which directly affects building expenses.
Peak demand is the highest point in the day at which a building draws electrical consumption. A facility’s monthly utility rates are largely determined by the power usage level at this time, so anything that can be done to drive usage down will significantly reduce utility costs. As evidenced by their test values, cool roofs are an effective way to decrease air conditioning loads during peak demand times.
Cool roof values are expressed in terms of solar reflectance and thermal emissivity. The combination of these values is used to determine how hot a surface will become by its ability to reflect solar energy and radiate heat away from itself. Cool roofsare capable of reflecting solar heat away from a building by more than 70 percent. In fact, the U.S. Environmental Protection Agency estimates that ENERGY STAR® qualified roofing products can lower roof surface temperatures by up to 50°F.
According to Jeff Steuben, executive director, and Carolyn Richter, communications manager, Cool Roof Rating Council (CRRC), in a recent Florida Roofing article, “Building occupants can experience improved comfort as compared to a conventional dark roof, as the building’s interior is subject to less thermal flux and stays cooler during warm seasons,” and, “Reduced indoor temperatures lead to energy savings from reduced cooling energy loads.”
Along these lines, contractors can also access a CRRC-provided listing of cool roof rebates, codes and voluntary cool roof programs at: www.coolroofs.org/resources/rebates-and-codes.
Cool Roofing Longevity
In addition to energy efficiency, cool metal roofs are known for extended durability and longevity, with most products offering a 40-year finish warranty.
In fact, a well-noted extensive study, Natural Exposure Testing in California, conducted by the Oak Ridge National Laboratory, found that pre-painted metal roofing maintained higher levels of reflectance, over a three-year period, due to its ability to shed particulate matter, as compared to conventional roofing materials. Further, pre-painted metal roofing has been found to retain 95 percent of its initial solar reflectance over this same three-year period.
Increasing performance and energy savings, solar reflective pigments in cool metal roofs offer higher total solar reflectance and thermal emittance, even in darker colors. With cool roof technology, the ability for the roof to store heat and radiate that heat into the building after sundown is dramatically reduced.
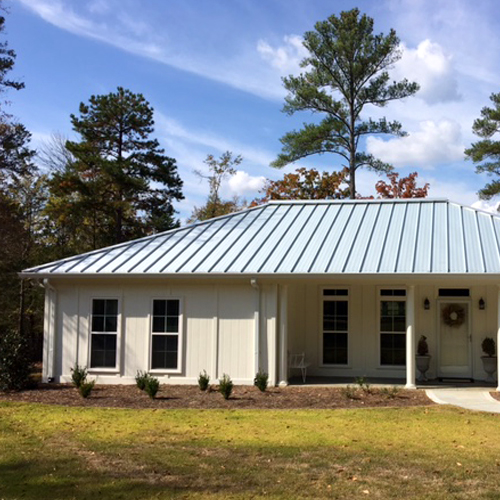
Cool metal roofs are proven to deliver environmental and performance benefits, of which the most significant to building owners is their contribution to the bottom line. Although savings will vary based upon geography, materials and insulation, the U.S. Environmental Protection Agency estimates that reflective roofs can save up to 40 percent of a building’s cooling energy costs.
When utilizing the U.S. Department of Energy’s Cool Roof Peak Calculator, contractors will discover that the total value of energy savings offered by a cool roof averages more than $1,000 annually in most climate zones for a typical commercial building. Furthermore, this applies to both cool roofing installed over both existing roof insulation and new insulation.
Proven Strategy
As established by documented study and significant heat build-up reduction levels, cool roofs are a proven strategy for supporting longer lasting roofs, reducing both utility costs and decreasing a building’s environmental footprint as Steuben and Richter conclude, “cool roofs are one of the most effective ways to obtain energy savings and environmental rewards through building envelope design and re-roofing projects.”