Tag: Double-Lok
Choosing Metal Roofing Types
All metal roofing is not the same. There are different profiles in different shapes for different reasons and to suit different performance needs. How to choose? Here’s the process that metal building engineers go through at MBCI to zero in on the most economical selection that will still meet the performance requirements of a particular metal roof project.
Snap Together Trapezoidal Panels
Offered by MBCI under the name Ultra-Dek®, the trapezoidal shape is among the best for channeling water off of the roof. However, because of this shape, it is most appropriate for typical sloped roofs with single plane roofs areas free of valleys or hips. It’s snap together installation makes it quick and easy to install economically with wind resistance capabilities adequate for many situations. It also carries basic air leakage and water penetration testing approvals.
Mechanically Seamed Trapezoidal Panels
For roofs that require a higher degree of performance than snap together systems can provide, MBCI Double-Lok® panels can be considered. The mechanically field-seamed, trapezoidal legs provide higher wind and water resistance with test results to satisfy UL-90, FM ratings, and Miami Dade County approvals. This makes them ideal for many industrial, commercial, and architectural roofs without hips and valleys that are subject to higher wind and rain demands. While the material cost for the panel is the same as for the Ultra-Dek®, there is more labor cost due to the mechanical field-seaming compared to the snap together installation. The Double-Lok® panel is also used often for retrofit installations over pre-existing metal roofs either to update the roof or to provide additional insulation. In either case, there is no need to disrupt the existing roofing or structure below allowing for a very cost-effective solution. Check with MBCI on the details of how to properly do a retrofit with these panels though to be sure things work out as intended.
Vertical Legs with Mechanical Seams
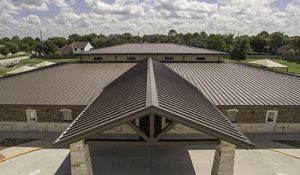
In cases where the trapezoidal legs aren’t appropriate or desired, then vertical leg, standing seam metal panels are the next logical choice. The MBCI BattenLok® HS system uses 2” tall legs that are mechanically field-seamed once along each panel joint to create a high strength, structural standing seam roof system that can be installed directly over purlins or bar joists – no additional solid substrate is required. It is also capable of transitioning from roof to fascia with the use of accessory seam covers.
Double Seamed Vertical Legs
In cases where very rigorous weather conditions may be encountered, the MBCI SuperLok® roof panels provide the highest degree of roof performance. While the manufactured SuperLok® roof panel is essentially the same as the single seamed BattenLok® panel, the profile is modified slightly to allow for standing seams to be rolled over twice, thus creating a stronger, thicker seal between adjacent panels. Once again, there is no difference in the material cost between the two, but the added field-seaming step will obviously add to the labor cost of this roof choice. Nonetheless, that can be a small price to pay for the higher performance and added peace of mind that the system offers.
While we have pointed out the differences between these four different metal roofing choices, note that there are some basic similarities too. They all use high grade steel in standard gauge thicknesses and they can all be specified in the same wide choice of colors. They are all offered in multiple panel widths, although check with the manufacturer to be sure the width you prefer is available for the specific panel selected. They all can be used for low slope applications down to ¼” per foot except for the retrofit solution which requires a 3:12 pitch. Finally, they all do have some minor variations in the profile which can help with the final desired appearance of the finished roof on the building.
To find out more about the differences in roof deck types and how to choose the best ones for on a metal roof that you are involved with, contact your local MBCI representative, and sign up for our newsletter to subscribe to our blog.
Proper Care and Usage of Roof Seamers
As more standing seam metal roofs are being installed than ever before, it is imperative for roofing contractors to have the proper tools when quoting jobs. Remember, a properly formed seam is important for aesthetics, weathertightness and wind uplift. With the right tools in hand for these complex installations, you can get the job done faster, better and with greater cost efficiency than your competitors.
Know Your Type
Seamer use depends on the type of metal standing seam panels on the project: double lock seam, symmetrical seam, one-piece snap-lock interlock and two-piece snap-lock interlock. You will need to identify the type of panel in order to choose the right seamer and confirm that you are using the right seamer for the job. The double lock seam, also known as a Pittsburgh seam, is double-folded, meaning the finishing seam is 180 or 360 degrees. This applies to MBCI’s Double-Lok® and SuperLok® panels. A single-lock seam is 45 or 90 degrees, such as MBCI’s BattenLok® HS and Curved BattenLok®.
Follow Manufacturer Instructions Explicitly
Adherence to the field manual instructions is critical to ensure proper installation that will not result in damage to the seamer and/or panels. It is critical to carefully read the manufacturer’s manual thoroughly before beginning the seaming operation, whether renting or buying the equipment. Not only will this give you the best possible result, but it can also save you the headache of incurring costs of replacing or repairing the seamer due to misuse.
Step-by-Step Guide to Pre-Seaming
- Locate field manual in the seamer box and review operational procedures.
- Locate power source and check against power requirements in field manual.
- Check seams for proper engagement.
- Clean dirt, debris and excess sealant from seams and panel surfaces to avoid interfering with the seaming operation.
- Panels should be seamed with an electric seaming tool as panels are being installed.
Keys to Seaming Success
- The seamer should be supplied or recommended by the manufacturer. Don’t assume another manufacturer’s seamer will work on the panels you are installing. For example, other manufacturers may have a panel similar to MBCI’s BattenLok® HS but that doesn’t mean that an MBCI seamer would work on any of those panels. It is important to use the seamer recommended for the specific product. It must be the proper seam for the engineering. That is if you don’t seam it properly, the manufacturer won’t know if its load charts and tables are accurate.As previously stated, carefully read and follow seamer instructions for proper results. You will need a properly formed seam to ensure you achieve the desired aesthetics and weathertightness as well as mitigating risk from wind uplift. The seamers are miniature roll formers and need to be installed in a very specific way.
- Take care of the seamer—don’t leave it out in the rain or in other weather conditions where it could suffer damage.
- If not forming seams properly, stop immediately and call the manufacturer or company providing the seamer
- If renting, when returning the seamer make sure all equipment is returned, i.e. hand crimpers or hand seamers.
For more information on MBCI seamers, please review the manuals for specific panel types.
Using Wind Clamps to Improve Wind Uplift on Standing Seam Metal Roofs
Among the most important factors to account for when specifying a standing seam metal roof are wind control and wind uplift. It is imperative to take the necessary measures to ensure the safety and efficacy of the metal roof. The wind clamp—an extruded piece of aluminum that is placed on the panel seams at clip locations—is one accessory that can be used to improve wind uplift characteristics on metal roofs, delivering substantial time and cost savings as these devices help mitigate risk of wind uplift and improve overall wind design.
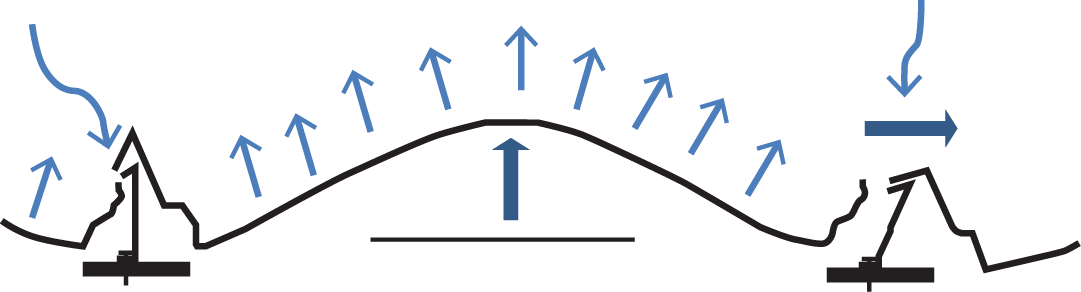
Why Use a Wind Clamp
A typical failure mode of a standing seam metal roof panel is the clip top pulling out of the panel seam when the panels are subjected to high winds. With a standard install of a standing seam panel, the seams just fold into each other. With enough pressure, wind will force seams to come apart—be it a vertical failure, horizontal movement of the seam or from clip disengagement. The clip top can then pull out of the panel seam.
The wind clamp resists the panel seam being opened, allowing for higher uplift loads. The purpose of wind clamps, in fact, is to prevent failures at the seam openings due to any deflection of the panel. The wind clamps provide more strength, thereby dramatically improving wind uplift performance.
The clamp is installed over the panel seam at clip locations, in the edge and corner zones of the roof. This allows the roof to resist the higher wind pressures in these zones, usually eliminating the need for additional purlins or joists. On large roofs, the savings can be substantial.
Another benefit is shorter installation time. Since additional purlins or joists are typically not required at the edge or corner zones of the roof, the building can be erected faster.
Choosing Wind Clamps
When choosing the type of wind clamp, it is important to consider the type of panel and the special features of the clamps. MBCI, for example, uses S-5!’s patented wind clamps, which work for two panel types—Ultra-Dek® and Double-Lok®. The S-5! wind clamps do not penetrate the steel, thereby eliminating the risks of corrosion and water leakage that can be introduced by a hole in the steel. Since the screws are hidden from the weather elements, it helps to maintain waterproofing.
Quantitative Difference with Wind Clamps
One of the biggest benefits of using wind clamps in the edge and corner zones is that usage minimizes the quantity of purlins needed, resulting in substantial cost savings. For example, let’s look at a comparison using MBCI’s Double-Lok 24” – 24 ga. panels with and without wind clamps.
In this example:
- The use of wind clamps in the edge and corner zones eliminated 3,800 linear feet of purlins.
- Assuming 8” x 2-1/2” Zee 14 ga. purlins were used, there would be a cost savings of $10,400.
Conclusion
Utilizing wind clamps to protect the investment of a standing seam metal roof can increase strength, make installation faster and lower overall cost.
Choosing the Right Type of Standing Seam Roof (SSR)
When it comes to specifying standing seam roofs, one type doesn’t fit all. While a standing seam metal roof system can be one of the most durable and weather-tight roof systems available in the industry, its benefits can be negated if you fail to understand the details in application parameters of the specific system. Do your research, though, and for your next design that requires an aesthetically pleasing and structurally sound metal roofing system, you can choose with confidence the standing seam metal roof system that suits your project to a tee.
How to identify a good standing seam roof system
A good standing seam roof system is one that can satisfy both the project’s specific design criteria and adhere to building code standards. Standing seam profiles can include those that are utilitarian or architectural in nature, are of numerous widths and profiles and have varying seam joinery (e.g., snap or field seamed).
Why specify a standing seam metal roof system
When properly installed, standing seam metal roof systems are an extremely effective and long-lasting material choice. Key advantages include:
- Weather-tight roofing system
- Can be engineered to withstand high winds (150 mph and higher)
- Class A Fire-resistance rating from UL
- Class 4 Impact-resistance rating from UL
- Long service life—up to 60 years
- Lightweight
- Special clips designed to accommodate thermal roof expansion and contraction and various thicknesses of fiberglass insulation
Matching the roof system to the project
In basic terms, there are four unique styles of metal standing seam panels: Double lock seam, symmetrical seam, one-piece snap-lock interlock and two-piece snap-lock interlock. These styles can be further delineated by seam shape or profile, i.e. trapezoidal rib, vertical rib, square rib and tee rib. The choice of the rib profile, as well as the rib spacing is generally an aesthetic preference of the designer. Knowing which style will best suit a given situation will help ensure a successful installation.
![]() |
||
---|---|---|
Some criteria to consider are roof slope, roof run (distance from eave to ridge), weather conditions (such as ice or snow) and architectural features, i.e. hips, valleys, dormers, parapet walls, etc.
For instance, if your project has a roof slope of 1/2:12 you will need to ensure the product being installed is approved for this low pitch. In this case, you would likely use a “double lock” or mechanically “field-seamed” panel. You also want to ensure that all details are able to provide for a weather-tight seal even if temporarily submerged during a heavy rain. Field-seamed panels are also the best choice in areas that experience heavy ice and snow.
Additionally, it is imperative to recognize complicated design details that should be carefully specified and reviewed regardless of the roof slope. Design conditions that require special attention include: roof transitions, dead valleys, dormers, eave offsets, ridge offsets and offsets in parapet walls.
It cannot be overstated that you should always consult a metal roofing manufacturer about the capabilities of the standing seam metal roof system, including what warranties are available, prior to specifying it.
Browse the standing seam product manual for more information.
Design and testing
Familiarize yourself with wind uplift testing as prescribed by Underwriters Laboratories (UL-90 – 580 Test) and ASTM E-1592.
MBCI Welcomes Insurance Institute of Building & Home Safety to Witness In-House Testing
To ensure our products perform as expected, MBCI conducts a variety of tests at our onsite laboratory in Houston, Texas. On April 16, MBCI and our parent company, NCI Building Systems, welcomed several researchers from the Insurance Institute of Building and Home Safety (IBHS) to our Houston headquarters to witness ASTM E1592 testing on MBCI’s standing seam roof panel Double-Lok. This test is designed to evaluate the structural performance of a standing seam roof system under uplift loading experienced by roofs during wind events.
IBHS conducts research to improve loss prevention-related design practices and better understand the risks of insuring buildings and homes. IBHS’s facilities include a full-scale wind tunnel in South Carolina which recently tested a 30’ wide, 50’ long building by our sister company, Ceco Building Systems, using the same standing seam roof system used in the E 1592 test. IBHS’s researchers joined our testing to observe how manufacturers test their own products so they may develop design-related loss prevention strategies which can help reduce insurance costs for consumers of metal roofing.
NCI’s Senior Research and Development Engineer Mark Detwiler, who was present at the testing, said “[IBHS] indicated that the test they witnessed reinforced that the industry rigorously tests their roof systems. They also noted that the failure mode they witnessed was consistent with what they have seen in their loss investigations, meaning that the test yields realistic, predictable results.”
Learn more about Double-Lok, ASTM E1592 testing and IBHS and their research efforts.